Ralte and Sailo have enabled the communities working on bamboo reduce manual labour
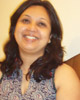
13-April-2015
Vol 6 | Issue 15
In a small village named Ratu in the tiny state of Mizoram lived a shy boy, Lalbiakzuala Ralte, who loved to draw and paint, and sing in the local choir.
In the same State, in Champhai town, a talkative, machine-crazy eleven-year-old, Lalpiangliana Sailo, built a room lighting system using just a torch bulb and battery for power-cut times, and later a river-water-operated grinder and husker.
![]() |
The machine fabricated by Sailo (left) and Ralte makes bamboo splints that are used to make products such as incense sticks, ice-cream sticks and toothpicks
|
From beginnings that sound somewhat like a folktale involving a miracle, together the two boys grew up to made headlines with their story. Their tale took shape in their small Aizawl workshop, where homegrown fabricators Ralte, now 47, and Sailo, 50, made a path-breaking human-energy-saving bamboo stripping and splint-making machine.
That, to cynical high-tech ears, may not sound as phenomenal as it truly is. To understand the significance of this innovation, you need to take a short virtual flight to Mizoram.
Once there, it will be evident to you that bamboo is one of the abundant natural resources of Mizoram. As much as 31 percent of the State’s land is under bamboo, of which as many as 27 species have been identified here.
Bamboo splints are used to make products such as incense sticks, ice-cream sticks and toothpicks, among others. Despite its varied uses, the potential of bamboo resources has barely been tapped, due to lack of sound management to develop its commercial viability.
It is not even known how many people are dependent on bamboo for their livelihood, though obviously many, many are. One major reason for the under-utilization of bamboo could be the splitting of bamboo by hand.
Yes, by hand: first the scanning of the plants to choose the right bamboo stems, followed by the tedious, time-consuming process of separating the ones without knots, and then the prolix and risky stripping and splint-making of bamboo using knives.
![]() |
The machine costs Rs 5,000 with transportation charges extra
|
Enter Ralte and Sailo, who had individually been developing customized tools and equipment on request or demand.
Ralte, an Arts graduate, became a fabricator after college, while also doing stints as a social worker in the Community Health Action Network (CHAN), a voluntary organization, and as an instructor for vocational training under World Vision.
Sailo’s school education, unfortunately, halted in Class V due to the extremist movement; later he tried his hand at different jobs including in carpentry, masonry, and fishing, and even at the electricity department.
Then he turned his full attention to innovations, with several useful machines to his credit, including a grass cutter, a vegetable/fodder chopper, a chicken-dressing machine and a dough-kneading machine.
The two had moved to Aizawl around the mid-1980s and met at CHAN’s Vocational Training Centre. It was here that Ralte and Sailo learnt about the abundance of bamboo in their tiny state and its uses. Their common interest in innovations, which had them occasionally discuss ideas with each other, now wove a good friendship.
Cut to 2006. An entrepreneur who manufactured incense sticks approached the two fabricators.
“Bamboo is the most desirable material for making incense sticks, and many individuals have been working in this field for years, but the process is full of drudgery,” said Ralte.
The entrepreneur wanted a manual machine that would both strip bamboo and make splints. The duo took up the challenge.
By 2007 they had opened a workshop and were ready. Ralte and Sailo were initially able to make a bamboo-stripper and a splint-making machine separately, with the research funded by the NEDFi (North Eastern Development and Finance Corporation).
However, such tools already existed. Their aim was to design an improved prototype that would merge the two functions successfully into one machine. At this point, their research was facilitated by a product development grant by NIF (National Innovation Foundation).
It took more than three months to build the first model. Research and trial chased each other’s tail. One prototype followed other, each with its own design challenges. Finally, Ralte and Sailo got fifth time lucky – they had a low-cost and efficient machine that was easily operable manually by a single person to slice bamboo strips and make splints from them.
What the user needed to do was to load the chosen bamboo stem onto the machine and slide the cutter to and fro using a handle, resulting in 1.2-mm-thin strips of bamboo.
Then about 50 of these strips are stacked and loaded onto the machine vertically. The cutter is again moved to and fro, ending in splints of the desired width. In this way, a person could make about 5,000 uniform splints an hour, a huge improvement on the knife method.
![]() |
It is estimated that bamboo workers can earn up to Rs.8000 a month using a single machine
|
The NIF then filed a patent in the fabricator’s names and provided financial support from its Micro Venture Incubation Fund (MVIF) to commercialize the production.
By now, Ralte and Sailo have sold more than 2,000 of these double-duty machines in the North-East and other hilly States with bamboo resources as well as in neighbouring Nepal and Bangladesh.
Enquiries are coming in from China, Brazil and Sri Lanka too. “The machine costs Rs 5,000 plus transportation and we do sell it directly,” say Ralte and Sailo, “but we cannot fulfil the demand. We would like to sell the technology to another manufacturer.”
It is both difficult and expensive to research and Innovate in Mizoram, which is under-facilitated and geographically isolated. Advanced machines such as milling, plastic moulding and lathe machines are not easily available, and the nearest city to get any machine parts is Kolkata.
The bamboo stripping and splint-making machine makes the job of the bamboo worker easier, quicker and safer, as well as more lucrative.
According to Ralte, father of four sons, a person could spend three hours in the forest collecting bamboo and do all the necessary splitting to the required size at the forest. He or she could thus avoid the wasteful transportation of unwanted and knotted pieces home.
Then he or she could collect at least 30 kilos of raw split bamboo. Assuming an hour of travelling, says Sailo, who has a daughter and two sons, the bamboo worker or any other family member could spend the remaining four hours (of an eight-hour workday) at home by making incense sticks.
After allowing for the margin of wastage for drying, the total quantity of dried and polished incense stick ready for sale would be 16 kilos, which would sell for about Rs 20 per kilo. That makes Rs 320 per day for the user of the machine. In a working month of 25 days, that would mean Rs 8000 a month, and good news for the bamboo worker.
Like fast-growing bamboo, projects grow and multiply. Ralte and Sailo are trying to make cheaper versions of bamboo stripper-cum-splint-making machine using plastic components.
Their betel-nut peeling machine has seen 16 trials already. More than 100 chicken dressing machines have been sold in the State. A banana-fibre extracting machine is a WIP (work in progress), among many others. This pair of innovators is obviously irrepressible.
Creativity is said to be a by-product of luxury, while innovation is driven by need. At unexpected coordinates, Ralte and Sailo came together to change the life of entire communities, easing their labours and reshaping their livelihoods.
As Roliana, 55, a bamboo worker from Thingsulthliah village, says, “With this machine, my production increased and I earn more money. I can slice bamboo accurately, even while watching television!”
There could not be a more heartfelt endorsement for Ralte and Sailo.